Related Posts
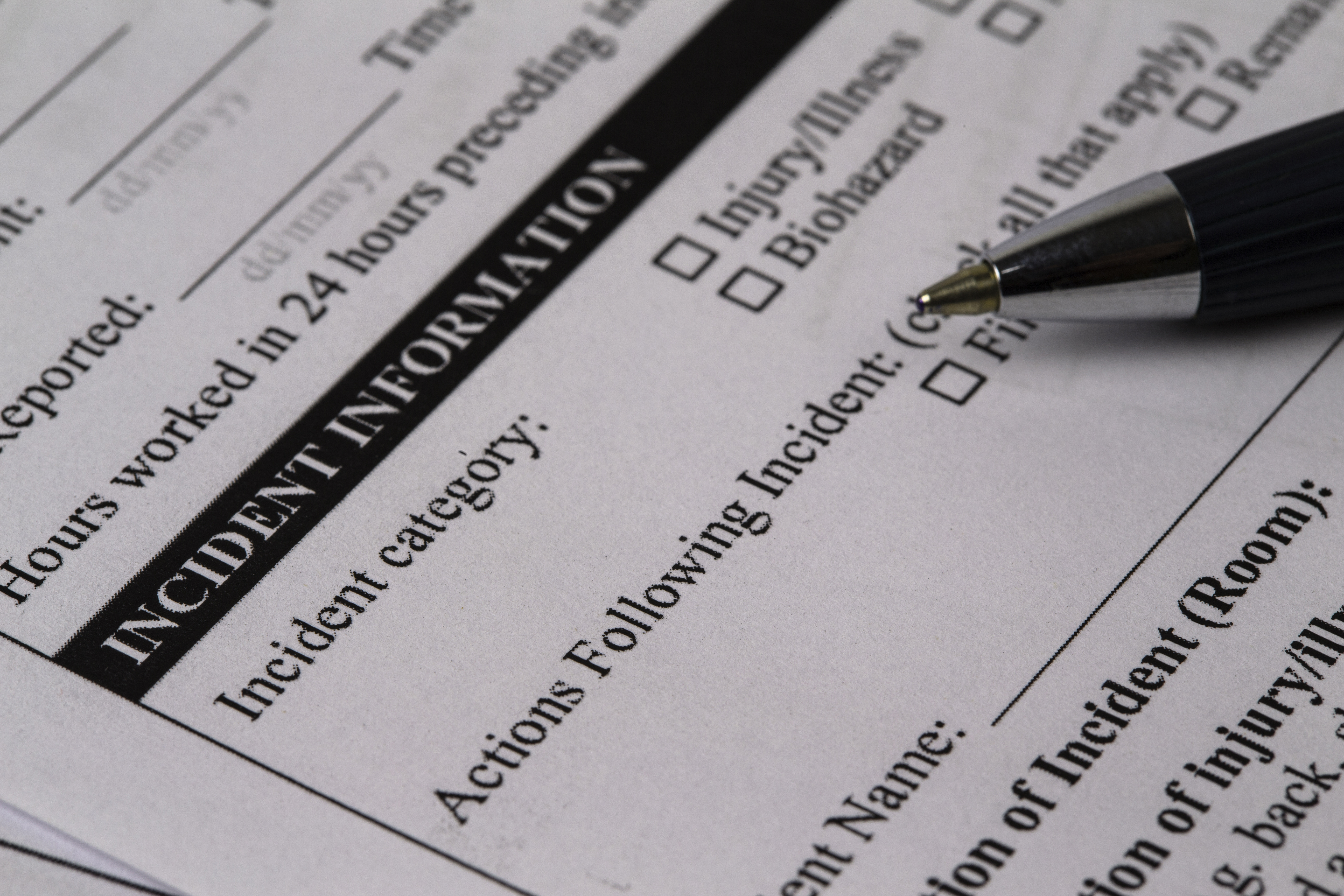
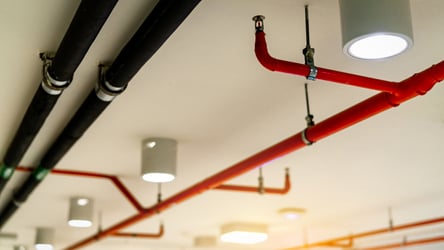
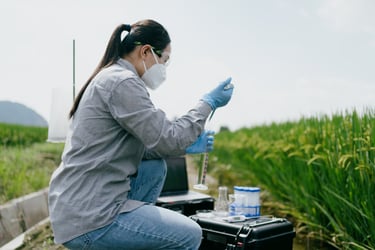
You are about to leave Risk Strategies website and view the content of an external website.
You are leaving risk-strategies.com
By accessing this link, you will be leaving Risk Strategies website and entering a website hosted by another party. Please be advised that you will no longer be subject to, or under the protection of, the privacy and security policies of Risk Strategies website. We encourage you to read and evaluate the privacy and security policies of the site you are entering, which may be different than those of Risk Strategies.
Editor’s note: This article summarizes a recent Risk Strategies webinar based on OSHA content. For additional details, please refer to OSHA's Job Hazard Analysis documentation, OSHA 3071.
Navigating OSHA regulations to maintain a safe work environment can seem daunting. However, a Job Hazard Analysis (JHA) offers a practical framework to safeguard your construction or manufacturing workforce. A JHA systematically identifies and addresses potential risks, so your team can perform their tasks confidently, without exposure to unnecessary dangers.
JHA is an occupational safety tool applicable across industries and work environments. It pinpoints potential hazards before they result in accidents by examining the relationship between workers, tasks, tools, and the environment. A JHA enables you to take proactive steps to eliminate or mitigate risks.
A well-executed JHA goes beyond meeting regulatory requirements by driving behavioral change at every organizational level to foster a safety culture.
Not all jobs present the same level of risk. While everyone can benefit from a JHA, focus first on jobs that:
By conducting a JHA, you help ensure your working environment is safe for all employees.
You might think a JHA is unnecessary if your worksite appears to have minimal or no hazards. But a closer examination of your employees' daily tasks might reveal hidden risks often overlooked. What may seem like routine or harmless aspects of the job could unexpectedly lead to a severe accident. Conducting a JHA helps uncover these potential dangers, ensuring proactive measures are in place to prevent incidents.
Hazards can arise from numerous sources:
By categorizing potential hazards, you can systematically evaluate your workplace and identify areas for improvement.
The first step in the JHA process is to recognize and accept that your workspace may contain hazards. From there, the process unfolds, with each step playing a vital role in identifying, mitigating, and ultimately controlling potential risks:
The hierarchy of controls phase comes during the eliminate hazards and implement control measures segment of the JHA. This framework from the National Institute for Occupational Safety and Health (NIOSH) helps you decide hazard mitigation strategies. You want to adopt the lowest number solution that’s feasible (1 is ideal):
While elimination and substitution are the most effective controls, they can be challenging to implement in existing operations due to the need for substantial process changes. As you design new processes, incorporating the right controls from the outset can prevent illness, injuries, and business interruption.
JHA is a transformative process that reduces operational risks. By systematically identifying hazards and implementing controls, you can protect your workers, improve efficiency, and maintain compliance with regulatory standards.
Find John on LinkedIn.
Connect with the Risk Strategies Risk Management Services team at safety@risk‐strategies.com.
The contents of this article are for general informational purposes only and Risk Strategies Company makes no representation or warranty of any kind, express or implied, regarding the accuracy or completeness of any information contained herein. Any recommendations contained herein are intended to provide insight based on currently available information for consideration and should be vetted against applicable legal and business needs before application to a specific client.