An automatic fire sprinkler system is a vital component of fire protection for residential and commercial properties. They help control or extinguish fires and save lives, but misconceptions exist regarding their operation, installation, and maintenance. Because sprinklers can make the difference between fire containment and total loss, ensure they're ready when you need them most. Here’s what you need to know.
Debunking fire sprinkler system myths
Fire sprinkler systems don’t always operate as shown in films and TV. In a real-life emergency, you want to know fact from fiction. Consider these pervasive myths:
- The manual fire alarm activates the sprinkler system: Pulling a fire alarm alerts the building’s occupants and fire department, but it doesn’t activate sprinklers.
- Smoke alone will trigger the sprinklers: Sprinklers are heat-activated, not smoke-activated. With most installations, each sprinkler head operates individually when the temperature reaches a specific threshold.
- All sprinkler heads activate simultaneously: In a typical system, only the heads directly exposed to high heat will activate. They work one at a time to control the spread of fire.
- Sprinkler system water is clean: The water in sprinkler pipes is often stagnant and may contain oil and rust.
- All sprinkler systems are the same: Specialists design sprinkler systems based on the characteristics of the building and activities happening inside. Different hazards require varying amounts of water and pressure to control a fire.
Different types of fire sprinkler systems
Unfortunately, there isn't a universal automatic fire sprinkler system that works in all situations. For example, a manufacturing facility needs something different from a warehouse or an office building. A sprinkler expert can help recommend the correct type for your specific environment and fire risks:
- Wet sprinkler systems are the simplest and most common variety. They're always filled with water, allowing for immediate discharge when a sprinkler head is activated by heat. These systems require the temperature in buildings to remain above freezing year-round.
- Dry sprinkler systems use pipes filled with pressurized air or nitrogen, with water held back at a control valve located in a heated area. When a sprinkler head activates, it releases air and fills the pipes with water, discharging onto the fire. They’re typical in unheated areas where the risk of freezing exists, such as attics or outdoor spaces.
- Pre-action sprinkler systems are similar to dry systems, but require an additional signal from a fire detection device before releasing water into the pipes. This dual-trigger system prevents accidental water damage. Organizations use them in environments with high-value equipment, such as data centers or art galleries.
- Antifreeze sprinkler systems use a glycol-based solution mixed with the water to lower its freezing point. Buildings use these systems in unheated spaces where freezing temperatures are a concern. However, due to issues with older antifreeze solutions contributing to fires, new regulations require specific, approved antifreeze formulations.
- Water mist systems use fine droplets of water, which reduce water damage while effectively controlling fires. They’re gaining popularity for high-value and sensitive areas like libraries, museums, and art galleries.
- Foam sprinkler systems smother flames, which is ideal for fires involving flammable liquids or high heat release rates. They work best in high-hazard environments, such as aircraft hangars or fuel storage facilities.
Residential vs. commercial fire sprinkler systems
There are two primary categories for sprinkler systems:
- Residential systems (NFPA 13R) focus on life safety. They give occupants enough time to escape the building rather than extinguish the fire. These systems use smaller sprinkler heads and piping, and the design requirements are less stringent than those for commercial systems.
- Commercial systems (NFPA 13) work for life safety and property protection. They control or extinguish fires, thus reducing damage to the building and its contents. Commercial systems use larger heads and piping.
Make sure to install and maintain the correct sprinkler system for your business.
Installation and design considerations
If you’re designing a new building or updating an existing one, prioritize installing a sprinkler system. Without an up-to-date system, you risk your organization’s bottom line if an accident occurs. In the planning process, gather the following information:
- Occupancy classification: What is the building used for, and what materials are stored?
- Building height: This affects the pressure requirements for the system.
- Water supply: What is the available water pressure and flow rate?
- Construction type: Building materials can impact the design of the sprinkler system.
For any new fire sprinkler system installation, include the following documentation and equipment to ensure you are compliant with industry standards:
- Hydraulic placard: This contains critical information about the system's hydraulic design. It verifies that the system is capable of delivering the necessary water pressure and flow rates to control or suppress a fire in the building.
- Spare sprinkler head cabinet: This is required in every new installation. According to fire safety standards, a minimum of six spare heads must be available at the facility. These spare heads ensure you can quickly restore the system if one or more heads activate or are damaged.
- A functional system test (or acceptance test): This proves the system works as designed before it is fully commissioned and turned over to the building owner. This includes testing the underground mains that supply water to the system and the above-ground piping within the building. It confirms the sprinkler systems can deliver water where and when needed.
- As-built drawings: These are detailed diagrams that show the exact layout of the sprinkler system as it was installed, including any deviations from the original design plans. These drawings are invaluable for future maintenance, inspections, and potential system modifications, providing a complete visual reference of the system's components and locations.
Staying up to date
A fire sprinkler system’s long-term functionality depends on regular inspection, testing, and maintenance. The following tasks can help ensure your system will work properly during a fire:
Sprinkler head testing
- All sprinklers: Test or replace after 50 years, and every ten years thereafter. After 75 years, test every five years.
- Dry sprinklers: Test or replace at 20 years, and every ten years thereafter.
- Extra-high temperature sprinklers: Test at 20 years, and every ten years thereafter.
- Fast response sprinklers (except ESFR and CMSA): Test at 25 years, and every ten years thereafter.
- ESFR and CMSA fast response sprinklers: Test at 20 years, and every ten years thereafter.
- Sprinklers in harsh environments: Test every five years.
Inspections
- Sprinkler heads, piping, and fittings: Check annually for corrosion, obstruction, debris, damage, etc.
- Sprinkler control valves: Inspect monthly if locked/supervised or weekly if unlocked/unsupervised.
- Pressure reducing valves: Evaluate quarterly to determine if valves are open, leaking, damaged, etc.
- Hose-valves: Inspect quarterly for general condition.
- Fire department connection (FDC): Inspect quarterly for general condition.
- Air compressor/nitrogen generator: Evaluate monthly.
Maintenance
- Sprinkler control valves: Test annually (supervisory signal: test quarterly).
- Dry-pipe/pre-action valves: Perform annual trip test, and full-flow trip test every three years.
- Waterflow alarms: Test semi-annually.
- Main drain: Test quarterly for those with downstream backflow preventers. If no backflow preventer, test annually.
- Fire pumps: Perform weekly churn test for diesel; monthly churn test for electric; and annual full flow performance test.
- Pressure reducing valves: Test full flow every five years.
- Backflow preventer assemblies: Test annually.
- Air compressor/nitrogen generator: Test annually.
Shutting down? Have an impairment management program
And as an additional measure, implement an impairment management program. This is a structured plan or procedure for whenever a sprinkler system is taken offline. A plan helps reduce risks during the offline period and ensures the system is restored as quickly as possible. Key aspects of an impairment management program include:
- Reducing hazards and risks during the shutdown: This might involve stopping certain hazardous activities or reducing operations in areas that rely heavily on fire protection.
- Tagging the shut-off system: Visibly mark shut-off valves or other components when a system is offline to indicate the sprinkler system is temporarily out of service.
- Notifying key parties: Tell the local fire department, insurance carriers, and the facility's emergency response team of the shut-off plan. These parties can offer guidance or additional protection measures during the impairment.
- Following insurance carrier protocols: Some insurance companies require notification for planned offline periods of any duration, while others may only require it if the system is down for more than eight hours. Know the expectations of your insurance provider(s), and familiarize yourself with the policy language. Failure to follow the insurer’s requirements can result in a claim denial if a fire occurs while your sprinklers are offline.
Knowing your automatic sprinkler systems: an essential lifeline
Whether you're installing a new sprinkler system or undergoing an inspection, knowing the ins-and-outs of the systems, and sifting through the misconceptions, will help protect your building and its occupants for years to come. Also, correct sprinkler installation and maintenance can make a difference in your property insurance pricing and terms. Prioritize safety by taking the necessary steps today.
Want to learn more?
Watch our recent webinar, Automatic Sprinkler Protection: Risk vs. Reward.
Find Amy on LinkedIn.
Connect with the Risk Strategies Loss Control and Safety Team at safety@risk‐strategies.com.
The contents of this article are for general informational purposes only and Risk Strategies Company makes no representation or warranty of any kind, express or implied, regarding the accuracy or completeness of any information contained herein. Any recommendations contained herein are intended to provide insight based on currently available information for consideration and should be vetted against applicable legal and business needs before application to a specific client.
Related Posts
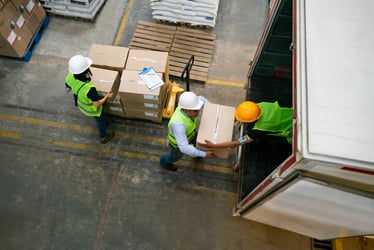
Using a Job Hazard Analysis to Meet OSHA Regulatory Requirements
Editor’s note: This article summarizes a recent Risk Strategies webinar based on OSHA content. For …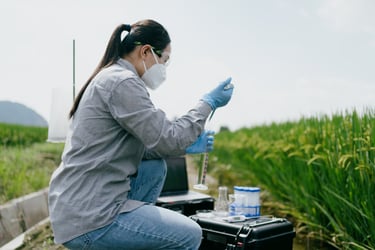